
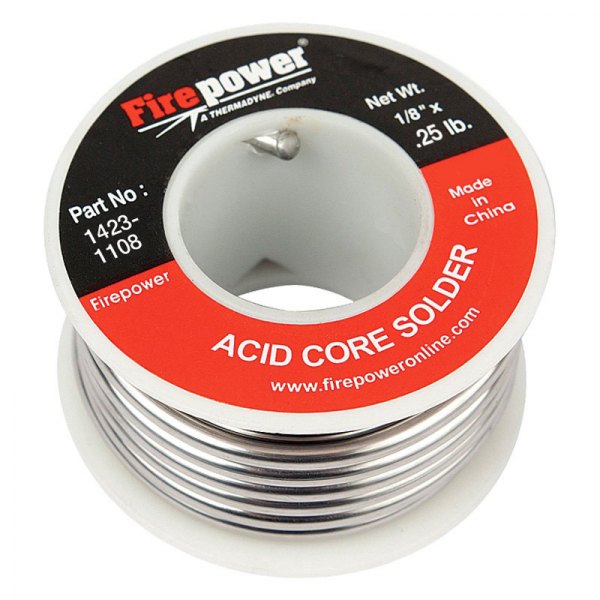
The acidic liquid flux converts the metal oxides to metal salts and water, which are typically locked up in the flux when it solidifies. The acidic liquid reacts with metal oxides, exposing clean metal for the solder to wet into. The rosin core of electronic solder will therefore melt before the solder, flowing into and around the joint. It has the advantage of being more or less inert at room temperature but highly acidic when liquified, and has a melting point slightly lower than solder. Rosin is a natural product derived from pine trees, notably the loblolly and longleaf pines for US-made rosin. Pre-cleaning the metals doesn’t cut it, by the time the solder flows atmospheric oxygen has rebuilt the metal oxide layer enough to spoil solder wetting.Įlectronic solder usually has a flux made of rosin. Fluxes are designed to remove metal oxides, and to do so while the joint is being soldered. Metal oxides are no good for solder joints - solder will not adequately wet a joint when there’s a metal oxide coating. The importance of flux is due to its ability to fight the mortal enemy of solder: metal oxides. But what exactly is flux and why do solder manufacturers go to the trouble of stuffing it into the core of solder wire? We all know that flux is critical to quality solder joints. There can also be voids within the intermetallic layer that add to mechanical instability. Intermetallics tend to be brittle, so if the intermetallic layer is too thick, the joint can be mechanically weak. Intermetallics are necessary to a good solder joint, but like so many things, too much of a good thing can be a bad thing. In most solders, the molten tin is the primary solvent that dissolves into the copper substrate and forms the intermetallic bond that electrically and mechanically stabilizes the joint. This creates intermetallic bonding and it’s the key to soldering. In the context of soldering, wetting is the process whereby the molten solder partially dissolves into the copper base metal, forming a region that’s part solder and part copper. For a soldered joint to be electrically and mechanically sound, the solder needs to wet the metals to be joined.
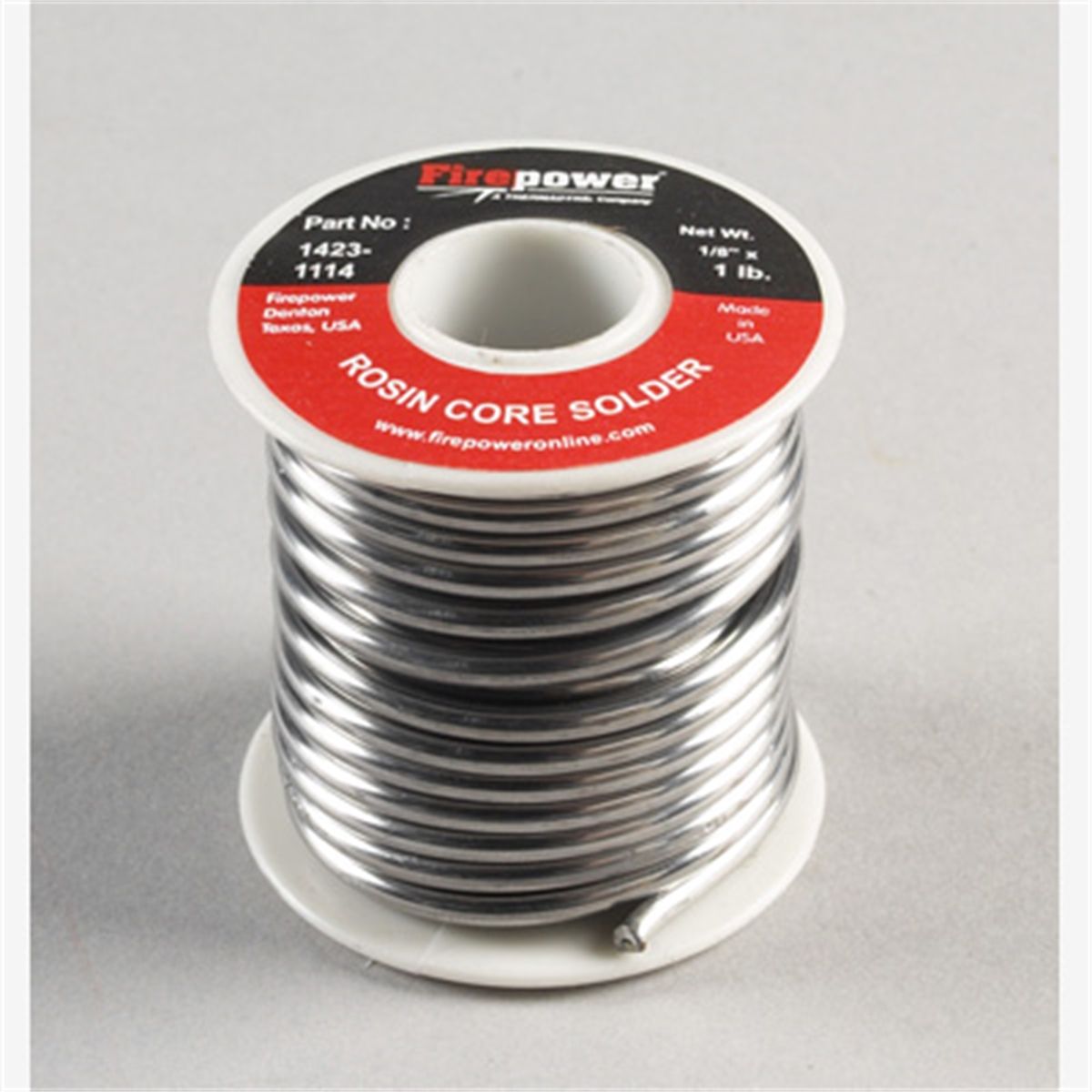
People seem to think of solder as some kind of “metal glue” - apply it as a liquid and let it become solid to lock a joint together. Solder needs to do more than just melt and solidify, though. In other words, solder needs to be strong enough to physically hold a joint together without introducing any undesirable electrical properties to the joint.
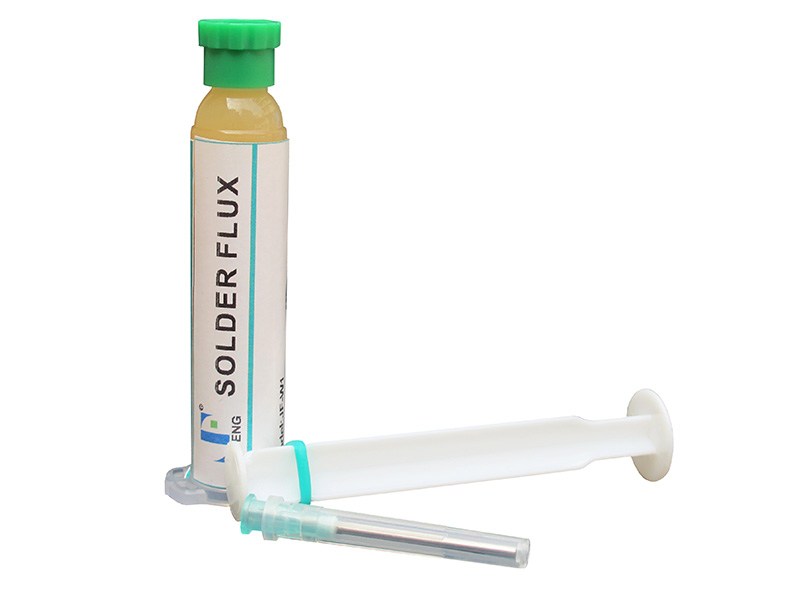
Solder needs to melt at a predictable temperature and maintain its mechanical and electrical properties when it solidifies. New regulations in response to environmental concerns have led to the development of different lead-free alloys, but whatever the composition, solder’s job is pretty simple. For electronics uses, the king of solders for years was an alloy of 60% tin and 40% lead. Solder is just an alloy that has been engineered to melt at a specific temperature. The metallurgical details of solder itself could take volumes to discuss completely, but for our purposes it’s pretty simple stuff. Brazing is similar to soldering in this regard even though the filler metal in brazing melts at a much higher temperature than solder, the joined metals still don’t melt. The metals being joined usually have a much higher melting point than the solder. Unlike in welding, only the filler metal - the solder - melts. Soldering is the joining of metals by melting a filler metal into the joint. It should come as little surprise that like other metal working methods, soldering has a strict definition. Seems like adding a little inside information might help me improve my skills, so I set about learning what’s going on mechanically and chemically inside a solder joint. I’m confident that I could make a good, strong, stable joint that’s both electrically and mechanically sound in just about any kind of wire or conductor.īut like some many of us, I learned soldering as a practical skill put solder and iron together, observe results, repeat the stuff that works and avoid the stuff that doesn’t. I won’t say that I’m the best solder-slinger around, but I’m pretty good at this essential shop skill - at least for through-hole and “traditional” soldering I haven’t had much practice at SMD stuff yet. I’ve been soldering for a long time, and I take pride in my abilities.
